Hiring the right SolidWorks professional is no easy task, especially when you need someone who can design, simulate, and analyze mechanical components. A skilled SolidWorks user can enhance product development, streamline workflows, and reduce errors, but how do you identify them?
This blog post provides a set of carefully curated SolidWorks interview questions for various experience levels, from basic to expert. We also include multiple-choice questions (MCQs) to help you gauge a candidate's theoretical knowledge and practical skills.
By using these questions, you will be able to filter out the best talent. To make your hiring process even more data-driven, consider using a technical aptitude test before the interview.
Table of contents
Basic SolidWorks interview questions
1. What's the first thing you do when starting a new SolidWorks project?
The first thing I do is define the project's scope and requirements clearly. This includes understanding the purpose of the design, its functional requirements, the target manufacturing process (e.g., machining, injection molding), material selection criteria, and any relevant industry standards or regulations. This clarity helps avoid rework later.
Next, I establish a well-organized file structure and naming convention for all parts, assemblies, and drawings. This ensures that all team members can easily locate and understand the project's data. Setting up custom properties within SolidWorks for things like material, part number, and description early on streamlines documentation and bill of materials creation.
2. Can you explain the difference between a part, an assembly, and a drawing in SolidWorks?
In SolidWorks, a part is a single 3D component, like a bolt or a bracket. It's the fundamental building block. An assembly is a collection of parts (and potentially other sub-assemblies) that are put together to form a more complex product or system. Assemblies define how the parts relate to each other and how they move, if applicable. Finally, a drawing is a 2D representation of a part or an assembly. Drawings are used for manufacturing and documentation, and typically include dimensions, tolerances, and other annotations needed to fabricate the part or build the assembly.
3. Describe the process of creating a simple extruded boss/base feature.
The process of creating a simple extruded boss/base feature typically involves these steps: First, a 2D sketch is created on a selected plane or face. This sketch defines the profile of the feature. Then, the 'Extrude Boss/Base' command is activated. This opens a dialog box (or panel) where the extrusion parameters can be set. Important parameters include the direction of extrusion and the extrusion depth or end condition (e.g., blind, through all, up to surface). Once these parameters are defined, the feature is generated based on the sketch, resulting in a 3D solid.
4. How would you create a hole in a solid body?
Creating a hole in a solid body depends on the context (CAD software, 3D modeling, programming, etc.). Generally, you'd subtract one solid body (representing the hole) from the original solid body. This is often called a boolean operation, specifically a 'difference' or 'subtraction'.
In CAD software, this is usually a direct feature. In programming contexts (e.g., working with mesh data), you might need to:
- Represent the solid bodies as meshes (e.g., using vertices and faces).
- Use a library or algorithm to perform the boolean subtraction (e.g., a Computational Geometry Library or custom code).
- The algorithm would identify intersecting faces, create new faces to define the intersection, and remove the geometry inside the subtracted volume.
5. What are some common file types used in SolidWorks?
SolidWorks utilizes several file types. Some common ones include:
.SLDPRT
: Part files, containing the 3D geometry of a single component..SLDASM
: Assembly files, containing the arrangement of multiple part files to create a complete product or sub-assembly..SLDDRW
: Drawing files, representing 2D engineering drawings derived from 3D parts and assemblies, often including dimensions, annotations, and bill of materials..STEP
/.STP
: Standard for the Exchange of Product Data, a neutral format for sharing 3D models between CAD systems..IGES
/.IGS
: Initial Graphics Exchange Specification, another neutral format for exchanging 2D and 3D data..STL
: Stereolithography, used for rapid prototyping and 3D printing, representing the surface geometry of a 3D object using triangles.
6. Explain how you would apply a material to a part.
Applying a material to a part depends heavily on the type of material and the desired outcome (e.g., visual appearance, protection, functionality). Generally, the process involves several steps:
- Preparation: Clean the part's surface to remove any contaminants like oil, dust, or rust. This might involve sanding, degreasing, or chemical etching.
- Material Selection: Choose the appropriate material based on the part's function, environment, and aesthetic requirements. Consider factors like adhesion, durability, and cost.
- Application Method: Select the correct application method. Options include spraying (paint, coatings), brushing (adhesives, sealants), dipping (plating, anodizing), powder coating, or vapor deposition. For example, painting requires careful masking, spraying multiple coats, and curing; adhesives require precise application and clamping.
- Curing/Drying: Allow the material to cure or dry according to the manufacturer's instructions. This may involve air drying, baking at specific temperatures, or using UV light.
- Inspection: Check the finished part for defects like uneven coating, bubbles, or scratches. If necessary, perform touch-ups or rework the part.
7. What's the purpose of using relations and dimensions in sketches?
Relations and dimensions in sketches are used to precisely define and control the geometry. Relations define geometric constraints between sketch entities (lines, circles, etc.), like making two lines parallel, perpendicular, or tangent. Dimensions, on the other hand, define the size of sketch entities (e.g., length of a line, radius of a circle) or the distance between them.
The purpose is to create robust and parametric designs. By using relations and dimensions, you can easily modify the design by changing dimension values, and the sketch will update accordingly while maintaining the intended geometric relationships. This avoids manual adjustments and ensures design intent is preserved during modifications. For example, in CAD software, you can define a rectangle with equal sides using an equal relation and then specify the length of one side using a dimension. Changing that single dimension will automatically update the other side, ensuring it remains a square.
8. Describe how you would create a fillet or a chamfer on an edge.
To create a fillet or chamfer, I'd typically use a CAD or 3D modeling software. For a fillet (rounded edge), I would select the 'fillet' tool, specify the edge(s) to round, and define the radius of the fillet. The software would then generate a smooth, curved transition between the adjacent faces.
For a chamfer (angled edge), I'd select the 'chamfer' tool, choose the edge(s), and define the chamfer's distance or angle. The software would then create a flat, angled face connecting the original faces. Some software might offer options for equal distance chamfers or chamfers defined by two different distances from the edge.
9. How do you create a pattern of features in SolidWorks?
In SolidWorks, you can create patterns of features using several methods. The most common are: Linear Pattern, Circular Pattern, Fill Pattern, Curve Driven Pattern, and Sketch Driven Pattern. You select the feature(s) you want to pattern, then define the pattern's parameters (e.g., direction, spacing, number of instances) based on the pattern type.
For example, using a Linear Pattern, you'd select the feature, specify the direction(s) for the pattern, the distance between instances, and the number of instances in each direction. SolidWorks then replicates the feature according to these parameters. Similar logic applies to the other pattern types, but with different defining parameters appropriate to the pattern's geometry (e.g., angle for Circular Pattern, boundary for Fill Pattern).
10. What is the feature manager design tree, and why is it important?
The FeatureManager design tree in SolidWorks (and similar CAD software) is a hierarchical, visual representation of the model's history and features. It shows how the part or assembly was built, listing the order of operations and features used (like extrudes, revolves, cuts, fillets, etc.).
It's important because it allows users to easily understand, modify, and troubleshoot the model. By navigating the tree, one can edit specific features, change their parameters, reorder them (which impacts the final design), or suppress/unsuppress them. This facilitates design changes, debugging, and understanding the model's construction logic.
11. Explain how to create a revolved feature.
A revolved feature is created by rotating a 2D profile around an axis. Imagine spinning a cookie cutter shape around a central stick - the space that it occupies is your revolved feature. To create it, you typically need a 2D sketch defining the shape and a line that will serve as the axis of revolution. The software then sweeps the profile around this axis for a specified angle (e.g., 360 degrees for a full revolution).
The process generally involves:
- Creating a 2D sketch of the profile. This sketch defines the shape you want to revolve.
- Defining an axis of revolution. This is the line around which the profile will be rotated.
- Specifying the angle of revolution. This determines how much the profile is rotated around the axis. Often set to 360 degrees for a complete revolution. Some features like revolved cuts and revolved surfaces work similarly.
12. What is a sketch plane, and how do you choose one?
A sketch plane is a 2D surface in 3D space where you create 2D profiles or sketches. These sketches serve as the foundation for creating 3D features (like extrudes, revolves, etc.). It's like drawing on a piece of paper before turning that drawing into a 3D object.
Choosing the right sketch plane is crucial for efficient and logical modeling. You typically select a plane based on the desired orientation of the initial feature. Common choices include the default orthogonal planes (XY, YZ, ZX), existing faces of the model, or user-defined planes created using reference geometry. Consider the overall design intent and how the feature will relate to existing geometry when making your selection.
13. Describe the steps involved in creating a simple assembly.
Creating a simple assembly typically involves these steps:
- Write the code: Create source code files (e.g.,
.cs
for C#) containing the classes, interfaces, or other types you want to include in your assembly. - Compile the code: Use a compiler (like
csc.exe
for C#) to compile the source code files into an assembly. The command usually specifies the output file name (assembly name) and the source files to be included. Example:csc /target:library /out:MyAssembly.dll MyClass.cs
- (Optional) Add AssemblyInfo: Create or modify the
AssemblyInfo.cs
file (or equivalent for other languages) to add metadata to the assembly, such as its name, version, culture, and description. This provides information about the assembly itself. - (Optional) Sign the Assembly: For strong-named assemblies, generate a key pair (using
sn.exe
), and use the compiler to sign the assembly with the private key. This ensures the assembly's uniqueness and prevents tampering. Example:csc /target:library /out:MyAssembly.dll /keyfile:MyKey.snk MyClass.cs
.
14. How do you add mates between components in an assembly?
In most CAD software (like SolidWorks, Fusion 360, etc.), you add mates between components in an assembly by selecting the 'Mate' feature. You then choose geometric entities (faces, edges, vertices, axes, planes) on the components you want to relate.
Common mate types include:
- Coincident: Aligns faces or planes.
- Concentric: Aligns axes of cylindrical features.
- Parallel: Makes faces or planes parallel.
- Perpendicular: Makes faces or planes perpendicular.
- Distance: Specifies a distance between faces or planes.
- Angle: Specifies an angle between faces or planes.
15. What's the difference between a fixed and a floating component in an assembly?
In an assembly, a fixed component has its position and orientation fully constrained, meaning it cannot move or rotate relative to the assembly's origin. It serves as an anchor. On the other hand, a floating component has some degrees of freedom and can move or rotate within the assembly's constraints. This movement is relative to the fixed or other constrained components.
Essentially, fixed components provide a stable reference point, while floating components can be positioned and move dynamically based on constraints defined within the assembly. Think of it like a foundation vs. parts that can be bolted onto that foundation with certain tolerances.
16. Explain how to create a drawing from a part or assembly.
To create a drawing from a part or assembly, you typically start within the CAD software (e.g., SolidWorks, AutoCAD, Inventor). Open the part or assembly file. Then, initiate a new drawing and select a drawing template or sheet size. The software will then allow you to insert views of the part or assembly onto the drawing sheet. You can control the view orientation (front, top, side, isometric, etc.), scale, and display style (e.g., hidden lines visible, shaded).
Once the views are placed, add dimensions, annotations (notes, callouts), and symbols to fully define the part or assembly. Most CAD packages allow for automated dimensioning and annotation tools. Finally, review the drawing for accuracy and completeness before saving or printing. Ensure all dimensions and annotations are clear, legible, and conform to any applicable drafting standards.
17. How do you add dimensions and annotations to a drawing?
Adding dimensions and annotations to a drawing depends heavily on the software or method being used (CAD software, hand drafting, etc.). Generally, dimensions are added using specific dimensioning tools within the software. These tools allow you to select points or lines on the drawing and automatically generate the dimension lines, extension lines, and dimension text displaying the measured distance or angle. Different types of dimensions exist, like linear, angular, radial, and diameter dimensions, each requiring a suitable tool.
Annotations include text, notes, symbols, and other explanatory elements. Text tools allow you to add labels and descriptions directly onto the drawing. Leaders can be used to connect annotations to specific features. Some CAD software allows for customizable annotation styles with pre-defined fonts, sizes, and symbols ensuring consistency throughout the drawing. Layer management is also important; putting dimensions and annotations on separate layers allows you to control their visibility and print settings independently.
18. What is a BOM, and how is it used?
A BOM (Byte Order Mark) is a special character (U+FEFF) that can appear at the beginning of a text file to indicate the encoding used, especially useful for UTF-16 and UTF-32 where byte order (endianness) matters. It's also sometimes used with UTF-8, though its necessity is debated as UTF-8's byte order is unambiguous.
BOMs are used by applications to correctly interpret the encoding of a file. While not always required, they can help applications automatically detect the encoding, particularly when multiple encodings are possible. However, some tools and programming languages can have trouble with BOMs in UTF-8 files, treating them as actual characters instead of encoding markers, which can lead to errors. Therefore, BOMs are generally avoided in UTF-8, especially for web-related content. Using editors that give you encoding options, you can save files as UTF-8 without BOM.
19. How do you change the units of measurement in SolidWorks?
To change the units of measurement in SolidWorks, go to Tools > Options > Document Properties > Units. Here, you can select from predefined systems like MKS (Meter, Kilogram, Second), CGS (Centimeter, Gram, Second), MMGS (Millimeter, Gram, Second), or IPS (Inch, Pound, Second). Alternatively, you can customize the units for length, mass, time, angle, etc., individually by selecting Custom and specifying the desired units from the dropdown menus.
Another way is via the document settings in the lower right corner of the SolidWorks window. By clicking on the unit system displayed (e.g., MMGS), you can directly access the Document Properties > Units page to make your selection.
20. What is the purpose of configurations in SolidWorks?
Configurations in SolidWorks allow you to create multiple variations of a part or assembly within a single file. This is useful for representing different sizes, materials, or features of a design without having to create separate files for each variation.
By using configurations, you can manage your design data more efficiently, reduce file clutter, and easily switch between different versions of your design for analysis, manufacturing, or presentation purposes. Configurations control parameters such as dimensions, features, materials and other properties.
21. Explain how to use the measure tool.
The measure tool allows you to determine distances and areas within a given environment, often a software application, image, or physical space. The exact method varies, but generally involves selecting the tool, then defining points or drawing lines to specify the dimensions you want to measure.
For example, in image editing software like Photoshop, you'd select the Measure Tool, click and drag on the image to define a line, and the tool would display the line's length in pixels or other selected units. In CAD software, similar methods are used to measure lengths, angles, and areas within drawings. Some tools also allow you to calibrate the scale first for accurate real-world measurements.
22. Describe how you would create a lofted feature.
To create a lofted feature, you'd typically start by defining multiple 2D profiles (cross-sections) at different planes. These profiles can be sketches, faces, or edges. The loft feature then interpolates smoothly between these profiles to create a 3D shape. You often need to specify guide curves or rails to control the loft's shape more precisely, especially for complex geometries. These guide curves dictate how the loft transitions between the profiles.
The software handles the actual interpolation. Most CAD systems provide options for controlling the loft's behavior, such as specifying tangency conditions or alignment methods. In many systems, you can also define start and end conditions to control how the loft terminates at the first and last profile. Lofting features are frequently used in creating complex curved surfaces.
23. What are some common sketching tools, and how are they used?
Common sketching tools include pencils, pens, markers, and digital drawing tablets with styluses. Pencils are often used for initial layouts and light sketching, allowing for easy erasing and adjustments. Pens and markers provide darker, more permanent lines, suitable for defining shapes and adding details. Digital tablets offer versatility with various brush types, colors, and undo options, making them ideal for iterative design and complex illustrations.
Sketching is a powerful communication tool, used to quickly explore ideas, visualize concepts, and communicate designs. It helps designers iterate rapidly, test different approaches, and refine their vision before committing to more detailed renderings or prototypes. The purpose can be quick user interface flows, architectural designs, or illustrating data flows for programming purposes.
24. Explain the difference between surface modeling and solid modeling.
Surface modeling defines the exterior boundary of an object, representing it as a skin without any information about its interior. It essentially consists of a set of surfaces that enclose a volume, but the volume itself is not defined. Solid modeling, on the other hand, defines both the exterior and interior of an object, providing a complete and unambiguous representation of its volume. It represents the object as a three-dimensional entity with properties like density and mass.
In simpler terms, imagine an empty bottle (surface model) versus a bottle filled with water (solid model). The surface model just describes the shape of the bottle, while the solid model also includes what's inside and how much it weighs. Solid models are used for applications requiring volume calculations, simulations, and manufacturing, while surface models are often used for visualization and aesthetic design.
25. How do you check for interferences in an assembly?
To check for interferences in an assembly, CAD software is commonly used. Most CAD packages have built-in interference detection tools. These tools work by calculating the space occupied by each component and identifying any overlapping volumes. The software then reports the clashes, often highlighting the interfering regions visually.
Different methods or settings can be used to define what constitutes an interference. These might include a 'hard' interference (actual physical overlap) or a 'soft' interference (clearance violations based on specified tolerances). Many packages also let you ignore specific interferences if they are intentional (e.g., press fits). Consider these points when using interference checking tools:
- Tolerance settings: Adjust tolerances to catch near misses.
- Component states: Consider different configurations or states of the assembly (e.g., moving parts through their range of motion).
- Software features: Learn about the specific interference checking features within your CAD software to use them effectively.
26. What is the purpose of design tables?
Design tables are primarily used to create multiple configurations of a part or assembly within a single file. Instead of creating separate files for each variation, you can use a design table (usually an Excel spreadsheet embedded or linked) to control dimensions, features, and other properties. This allows for efficient management and modification of similar designs.
By using design tables, you can quickly generate different versions of a model by simply changing values in the table. This streamlines the design process, reduces file clutter, and makes it easier to maintain consistency across related parts or assemblies. They are essentially a powerful way to parameterize your designs and automate the creation of variants.
27. Describe how to use the shell feature.
The "shell" feature typically refers to a command-line interface (CLI) used to interact with an operating system. It allows users to execute commands, run programs, and manage files using text-based input.
To use a shell, you first need to open a terminal or console application. Then you type commands and press Enter to execute them. Here are some common actions:
- Navigation: Use commands like
cd
(change directory) to move between folders. - File Management: Use
ls
(list),mkdir
(make directory),rm
(remove),cp
(copy), andmv
(move) for file operations. - Program Execution: Type the name of a program to run it. For example,
./my_program
. - Piping and Redirection: Use
|
to pipe the output of one command to another and>
or<
to redirect input and output.
28. How do you create a swept feature?
To create a swept feature, you need a profile (a 2D shape) and a path (a 2D or 3D curve). The profile is swept along the path to create the 3D feature. Most CAD software provides a sweep feature that allows you to select the profile and the path. Some systems also need a guide curve or surface to control the orientation and scaling of the swept profile.
The general steps are:
- Create a profile (sketch) - the shape you want to sweep.
- Create a path (sketch or 3D curve) - the trajectory along which the profile will be swept.
- Invoke the sweep command.
- Select the profile and the path. Ensure that they are on intersecting planes.
- Adjust options, such as alignment, orientation, and scaling if available.
29. What is the Center of Mass and how do you calculate it in Solidworks?
The Center of Mass (COM) is the point representing the average location of the mass of an object or system. It's the point where the object would balance perfectly if supported. In SolidWorks, the COM is calculated based on the geometry and material properties assigned to the part or assembly.
To calculate the COM in SolidWorks, you can use the 'Center of Mass' feature. This feature analyzes the part or assembly's geometry and assigned densities (materials) to determine the COM location. You can access this feature via Insert > Reference Geometry > Center of Mass. Once calculated, SolidWorks will display a point representing the COM. The coordinates of this point can also be accessed through the feature properties or by using SolidWorks API for more programmatic access.
Intermediate SolidWorks interview questions
1. Describe your experience with creating and using design tables in SolidWorks.
I have experience creating and utilizing design tables in SolidWorks to manage configurations of parts and assemblies. I've primarily used them to control dimensions, features, and material properties based on different configurations, enabling efficient management of product variations. For example, I've created design tables to manage the length and diameter of a bolt based on size specifications, or the material of a housing based on environmental requirements. This involved inserting a table (typically an Excel file) into the SolidWorks part or assembly, linking specific parameters to columns in the table, and then defining each configuration as a separate row.
I've also used equations and conditional statements within the design table to drive more complex relationships between parameters. For instance, if the bolt diameter is greater than a certain value, a specific thread type is automatically selected. I'm familiar with troubleshooting common issues, such as mismatched header names, incorrect units, and broken links. I also have some exposure to automation possibilities using VBA or SolidWorks API to programmatically update or create design tables.
2. Explain the difference between a sketch-driven pattern and a feature-driven pattern.
A sketch-driven pattern focuses on the overall structure and initial layout of the user interface. It prioritizes the high-level user flow and visual design, often starting with hand-drawn sketches or low-fidelity prototypes. The features are then built to fit within this established framework. The primary goal is to ensure a cohesive and intuitive user experience from the outset. This might involve tools like wireframing and prototyping software.
Feature-driven development, on the other hand, emphasizes building individual features independently, with less initial emphasis on the overall structure. The features are often developed and tested in isolation, and then integrated later. While faster to implement individually, feature-driven approaches can sometimes result in inconsistencies in the user experience or a fragmented interface. It might involve tools like Jira and Agile development practices.
3. How would you approach modeling a complex curved surface in SolidWorks?
To model a complex curved surface in SolidWorks, I'd typically start with a surface modeling approach. I would begin by sketching 2D profiles that define the overall shape of the curve. Splines are very useful here, allowing for smooth, controlled curves. Then, I'd use surface features like Lofted Surface
, Swept Surface
, or Boundary Surface
to create the 3D surface. These features require guide curves and profiles to shape the surface accurately. I might also use Fill Surface
to patch gaps. Finally, use surfacing tools like Knit Surface
to combine multiple surfaces into one continuous surface, and then Thicken
it if a solid body is desired.
Another approach involves using reference geometry like planes and axes to control the shape and orientation of the curves and surfaces. For very complex shapes, I might consider importing data from external sources, such as scan data or other CAD software, and use SolidWorks tools to refine and integrate the imported geometry. Using equations is also helpful to directly control curve shapes when possible.
4. What are the advantages and disadvantages of using configurations in SolidWorks?
Configurations in SolidWorks allow you to create multiple variations of a part or assembly within a single file. Advantages include reduced file clutter, easier management of similar designs, and the ability to create a family of parts/assemblies with different dimensions, features, or materials. This simplifies design changes and allows for efficient creation of part catalogs.
Disadvantages can include increased file size due to storing multiple configurations, potential for confusion if configurations are not named and organized effectively, and a steeper learning curve compared to managing individual files. More complex models with many configurations can also become slower to regenerate.
5. How do you manage revisions and versions of SolidWorks parts and assemblies?
SolidWorks revisions and versions are typically managed using SolidWorks PDM (Product Data Management) or SolidWorks Manage. These systems provide a central vault for files, control access, and automate workflows for releasing and revising parts and assemblies. Version control ensures that previous iterations are maintained and accessible. Revisions indicate significant changes after a design is released and are typically denoted by letters (A, B, C) or numbers.
Without PDM, a manual system involving folder structures and file naming conventions (e.g., Part-123_RevA, Part-123_RevB) can be used. This is less robust but can be adequate for smaller projects. Utilizing drawing templates with revision tables that are manually updated is also part of this approach. It is important to also use notes within drawings to describe the changes made for a specific revision.
6. Explain the purpose and use of equations in SolidWorks.
Equations in SolidWorks serve to create mathematical relationships between dimensions, properties, and features within a model. They allow you to drive the value of one parameter based on the value of another, ensuring design intent is maintained during modifications. This parametric control is crucial for efficient design iterations and automated updates.
The equations are used to link dimensions, part properties, and feature parameters. For example, the length of a rectangle could be defined as twice its width using an equation. When the width is changed, the length automatically updates according to the equation. SolidWorks equations support a variety of mathematical operations and functions, offering flexible control over the model's geometry and behavior. They can be global variables, linked to external files or specific to a component.
7. Describe your experience with sheet metal design in SolidWorks.
I have experience using SolidWorks for sheet metal design, including creating parts from scratch and converting existing solid models. I'm familiar with features like base flanges, edge flanges, hems, and bends, and I know how to apply forming tools and create flat patterns for manufacturing. I understand K-factor and bend allowance calculations and can configure these settings in SolidWorks to accurately represent material behavior. I've also worked with different sheet metal gauges and materials.
8. What is the difference between surface modeling and solid modeling in SolidWorks?
Surface modeling in SolidWorks focuses on defining the outer boundaries of a part using surfaces, which are essentially infinitely thin. It's great for creating complex shapes and aesthetically pleasing designs where internal volume isn't crucial. You can't directly calculate mass properties from a surface model until it's converted to a solid.
Solid modeling, on the other hand, represents a part as a fully defined 3D volume. This means SolidWorks knows the material and the space it occupies. Solid models are essential for simulations, manufacturing, and creating detailed engineering drawings because they allow for mass property calculations (weight, volume, etc.) and interference checking. Solid models are composed of features added to a base feature, and typically use sketches that are extruded, revolved, swept, etc.
9. How do you create and use custom weldment profiles in SolidWorks?
To create custom weldment profiles in SolidWorks, first sketch the desired profile on a plane. Save the sketch as a SolidWorks Library Feature Part (.SLDLFP
) in a designated weldment profile folder. The folder structure is important; typically, it's SolidWorks/lang/english/weldment profiles/<Standard>/<Type>
. For example, SolidWorks/lang/english/weldment profiles/MyStandard/MyProfileType/MyCustomProfile.SLDLFP
. SolidWorks searches these folders for weldment profiles.
To use the custom profile, start a new weldment structure. When defining the structural member, select the appropriate standard (e.g., 'MyStandard'), type (e.g., 'MyProfileType'), and then choose your custom profile ('MyCustomProfile'). The profile will then be used to create the weldment member along the sketched lines. You may need to adjust the profile's alignment and orientation using the 'Locate Profile' and 'Angle' options in the Structural Member PropertyManager.
10. Explain how you would simulate a simple mechanism using SolidWorks Motion.
To simulate a simple mechanism in SolidWorks Motion, I would start by creating the parts of the mechanism in SolidWorks CAD. Then, I'd assemble the parts using mates to define their relative positions and allowed degrees of freedom. Next, within the Motion Study environment, I would define the type of motion analysis (e.g., motion analysis with forces, or basic animation). Crucially, I'd apply forces or motion drivers to the mechanism, such as a motor or a linear actuator, to initiate movement. Finally, I'd run the simulation, analyze the results, and iterate on the design if needed to achieve the desired motion characteristics.
Specifically, setting up a four-bar linkage would involve modeling the links and joints, mating the joints for revolute motion, and applying a motor to one of the links. The simulation would then show the motion of the coupler link. I'd examine plots of position, velocity, and acceleration to understand the mechanism's performance. For something like a slider-crank, the approach would be similar, using appropriate mates to create the sliding joint.
11. Describe your experience with importing and exporting different file formats in SolidWorks.
I have experience importing and exporting various file formats in SolidWorks, including commonly used formats like STEP, IGES, STL, Parasolid, and DXF/DWG. When importing, I pay attention to import diagnostics to identify and resolve any potential issues with the geometry or data integrity. For exporting, I select the appropriate format based on the recipient's software and intended use of the file. For example, I use STL for 3D printing and STEP for general CAD exchange. I am familiar with the export options available in each format, such as setting the resolution for STL files or choosing which entities to export in a DXF/DWG file. I have also used SolidWorks' feature recognition tools to convert dumb solids into feature-based models during the import process.
12. How do you troubleshoot common errors when creating features in SolidWorks?
When troubleshooting SolidWorks feature creation errors, I start by carefully examining the error message itself. It often provides clues about the problem's origin (e.g., self-intersecting geometry, insufficient constraints, invalid input values). I then systematically review the feature's definition, checking the sketch for errors like open contours or overlapping lines. Dimensional accuracy and adherence to design intent are crucial. I also use tools like 'Check Sketch for Feature Usage' to identify potential problems with sketch geometry.
Common issues include incorrect feature types for the desired outcome, conflicting relations, and geometric singularities. If a feature fails, I'll often simplify the sketch or feature definition to isolate the problem. Sometimes, rebuilding the model or suppressing and un-suppressing the feature can resolve unexpected issues. For more complex errors, I will consult the SolidWorks help documentation or online forums for similar cases.
13. Explain the purpose and use of library features in SolidWorks.
SolidWorks Library Features are pre-designed, commonly used features (like holes, slots, ribs, or grooves) that can be easily inserted into different parts. Their primary purpose is to save time and ensure design consistency across multiple parts or projects. Instead of recreating the same feature repeatedly, you can simply drag and drop a Library Feature from the Design Library into your model.
The use of Library Features involves selecting a feature from the Design Library, positioning it on a target face or feature of your model, and then defining the necessary dimensions or parameters using pre-defined reference points or geometry. This significantly streamlines the modeling process and reduces the potential for errors.
14. Describe your experience with creating and using custom properties in SolidWorks.
I have experience creating and using custom properties in SolidWorks to manage metadata associated with parts, assemblies, and drawings. I typically use the Property Tab Builder to create custom input forms for users to easily add and modify properties like material, part number, description, revision, and vendor. These properties are then linked to drawing title blocks and bills of materials, ensuring consistency and accuracy across documentation. I also use SolidWorks API with VBA to automate the process of setting and updating custom properties, especially when dealing with large assemblies or needing to integrate SolidWorks with other systems.
For example, I wrote a VBA macro that automatically populates the 'Weight' custom property of a part based on its material and volume calculated by SolidWorks. The code retrieved material density from a lookup table and used the swModel.GetVolume()
method to compute the weight. This ensured accurate weight data for downstream processes like FEA and ERP systems. Below is the code example:
Dim swApp As Object
Dim swModel As Object
Set swApp = CreateObject("SldWorks.Application")
Set swModel = swApp.ActiveDoc
Dim volume As Double
volume = swModel.GetVolume()
'-- Code to get material and lookup density --
'-- Code to calculate weight = volume * density --
swModel.CustomInfo2 "", "Weight", CStr(weight)
swModel.Save
15. How would you optimize a SolidWorks assembly for performance?
To optimize a SolidWorks assembly for performance, several strategies can be employed. First, simplify parts by suppressing or removing unnecessary features like fillets, chamfers, or complex patterns. Utilize lightweight mode to load only the graphical data of components, significantly reducing memory usage and load times. Consider using derived configurations or simplified representations for complex parts when high detail isn't required. Also, ensure proper mate strategies - avoid over-defining mates, use standard mates where possible, and minimize in-context features which can cause rebuild issues.
Furthermore, regularly evaluate assembly performance using the 'Assembly Visualization' tool to identify performance bottlenecks caused by complex parts or excessive mates. Explore using large assembly mode when dealing with thousands of components. Regularly update graphics drivers. Suppress parts that are not visible or needed for the current task. Lastly, ensure your system meets the recommended hardware requirements for SolidWorks to prevent performance issues related to inadequate resources.
16. Explain the difference between a local and a global variable in SolidWorks equations.
In SolidWorks equations, a local variable is defined and used only within a single equation or feature. Its scope is limited to that specific equation/feature where it's defined. It's typically used for temporary calculations or intermediate values within that equation. It cannot be accessed or referenced by other equations or features.
On the other hand, a global variable (often referred to as a global variable in SolidWorks) is defined and stored in the 'Global Variables' folder in the FeatureManager Design Tree. These variables can be accessed and used by any equation or feature within the entire SolidWorks model. This allows you to define a single value and reuse it across multiple parts or features, ensuring consistency throughout the design. Modifications to a global variable propagate to all linked equations.
17. Describe your experience with creating and using SolidWorks macros.
I have experience creating and utilizing SolidWorks macros to automate repetitive tasks and streamline design workflows. I've used the VBA (Visual Basic for Applications) editor within SolidWorks to write macros for tasks such as generating BOMs, automating drawing creation, and modifying part properties in batches.
For example, I created a macro that iterates through all parts in an assembly, extracts specific custom properties (like material, vendor, and cost), and exports this data to a CSV file, automating what was previously a manual process. I've also used macros to automatically generate drawing views based on predefined templates and configurations. I understand the SolidWorks API and its object model which enables me to create robust and efficient macros. I am familiar with debugging and troubleshooting VBA code within the SolidWorks environment. I have also used the recorder to capture actions and then modify the VBA code to suit the task.
18. How do you handle large assembly performance issues in SolidWorks?
To handle large assembly performance issues in SolidWorks, I would focus on several key strategies. First, simplify the assembly by using lightweight components (suppressed features, simplified geometry), and utilize display states to control component visibility. Evaluate mate performance, replacing complex mates (like path mates) with simpler ones where possible and ensuring mates are fully defined to avoid redundant calculations. Consider using Large Assembly Mode, which automatically optimizes system settings for large assemblies. Regularly use SolidWorks Performance Evaluation tool to identify bottlenecks and optimize rebuild times.
Further steps involve optimizing hardware (RAM, SSD), using Defeature tool to create simplified versions of complex parts for assembly context, and applying SpeedPak configurations to reduce graphics processing overhead. It's also critical to enforce disciplined modeling practices, such as avoiding in-context features that create unnecessary dependencies and ensuring parts are created efficiently from the start. Also, leverage proper layering to suppress unnecessary complex components. Periodically purge unused features and configurations.
19. Explain the purpose and use of SolidWorks Routing.
SolidWorks Routing is an add-in that allows users to create and manage specialized types of assemblies that contain pipes, tubes, electrical cables, and harnesses. Its primary purpose is to automate the design and documentation of these systems, reducing manual effort and ensuring accuracy. It achieves this by providing tools for: creating routes based on predefined or user-defined specifications, automatically generating bills of materials and cut lists, and managing design changes effectively.
The use of SolidWorks Routing improves design efficiency, reduces errors, and allows for the easy creation of accurate manufacturing documentation for piping, tubing, and cabling systems. Key areas of use include industries like automotive (harnesses), aerospace (hydraulic lines), and process industries (piping systems).
20. Describe your experience with using SolidWorks Simulation for basic stress analysis.
I have used SolidWorks Simulation for basic stress analysis on several projects. My experience primarily involves performing static studies to determine the stress and displacement of parts under various loading conditions. I'm familiar with applying fixtures, forces, and pressure loads, as well as defining material properties. I also have experience with mesh generation and refinement to ensure accurate results.
I understand how to interpret stress plots, displacement plots, and factor of safety plots to identify potential failure points. I've used these simulations to optimize designs by identifying areas where material can be reduced without compromising structural integrity. My focus has been on validating designs against expected loads and ensuring they meet safety requirements.
21. How would you create a family of parts with different dimensions using SolidWorks?
There are several ways to create a family of parts with different dimensions in SolidWorks. The most common methods are using Design Tables and Configurations.
With Design Tables, you embed an Excel spreadsheet within your SolidWorks part file. This table lists the different dimensions and features you want to vary across the family, along with the corresponding values for each instance. Each row in the table represents a different configuration. Configurations, on the other hand, are variations of a part within a single file. You can manually create each configuration and modify dimensions and features individually, or you can drive them using a design table. You can also use equations and global variables to link dimensions and ensure consistent scaling across the family. Another option is using SOLIDWORKS DriveWorksXpress for a rules-based configuration.
22. Explain the difference between a derived part and a mirrored part in SolidWorks.
A derived part in SolidWorks is created by inserting one part into another, effectively creating a link between the base part and the derived part. Any changes made to the base part will propagate to the derived part. You can selectively include features and bodies from the base part, and even scale or transform them in the derived part. Essentially, it's a way to reuse geometry and maintain a parent-child relationship.
A mirrored part, on the other hand, is specifically a mirror image of the original part. It creates a new part file, and similarly to derived parts, it can maintain a link to the original. Changes in the original part will update the mirrored part, preserving the mirrored relationship. The key difference is that mirrored parts create a true reflection, while derived parts offer more flexibility in which features are incorporated and how they are transformed.
23. Describe how you would use SolidWorks to create a mold for a plastic part.
To create a mold for a plastic part in SolidWorks, I would first ensure the part design is finalized and properly drafted with appropriate draft angles for easy ejection from the mold. I would then use the Mold Tools to analyze the part for manufacturability and identify the parting lines and surfaces. After that, I would create the parting surfaces, shut-off surfaces and core and cavity blocks. Finally, I would use the tooling split feature to separate the core and cavity, and add features like runner system, gates, ejector pins, and cooling channels based on design requirements.
I would use the Mold Analysis tool to simulate the injection molding process, check for potential issues such as sink marks or weld lines, and optimize the mold design for efficient production. I will also document each step carefully.
24. How do you create and manage Bills of Materials (BOMs) in SolidWorks assemblies?
In SolidWorks, BOMs are created directly from the assembly structure. You can insert a BOM table into a drawing of the assembly via Insert > Tables > Bill of Materials. SolidWorks automatically populates the table based on the components in the assembly and their properties. You can customize the BOM by adding/removing columns (like part number, description, material), sorting, and filtering components. Configurations can be used to control which components are included in the BOM for different variations of the assembly. Item numbers are automatically assigned but can be manually overridden.
BOM management involves linking component properties to custom properties, which are then used in the BOM table. This ensures data consistency. For advanced management, consider using SolidWorks PDM or other PLM systems to control revisions, approvals, and BOM variations. These systems can automatically update BOMs when design changes occur, reducing errors. You can also export BOMs to various formats (e.g., Excel, CSV) for use in other systems like ERP or MRP.
Advanced SolidWorks interview questions
1. Explain the difference between surfacing and solid modeling in SolidWorks, and when would you choose one over the other?
Surfacing and solid modeling are two distinct approaches to creating 3D geometry in SolidWorks. Solid modeling creates objects with defined volume and mass, representing real-world physical objects directly. Surfacing, on the other hand, creates objects defined by their outer surfaces, which may or may not enclose a volume. Think of a solid model like a block of steel and a surface model like a thin sheet of metal.
You'd typically choose solid modeling for parts requiring accurate mass properties, interference checking, or manufacturing processes like machining. Surfacing is better suited for complex, organic shapes like car bodies, consumer product housings, or for creating tooling where complex parting lines are needed. You often combine both techniques: using surfacing to create the overall shape, then thickening it into a solid for further design or manufacturing.
2. How would you approach designing a complex curved surface in SolidWorks, ensuring it meets specific aesthetic and functional requirements?
When designing a complex curved surface in SolidWorks, I'd start by clearly defining the aesthetic and functional requirements. This includes understanding the desired look, any critical dimensions, and the surface's role in the overall design. I would then strategically select the appropriate surfacing tools such as lofted surfaces, boundary surfaces, or swept surfaces based on the specific geometry I'm trying to achieve.
Next, I'd use sketches and guide curves to precisely control the shape of the surface. I would pay close attention to surface continuity (G1, G2, or even G3) to ensure smooth transitions and avoid undesirable highlights or reflections. Finally, I would use surface analysis tools like zebra stripes and curvature combs to evaluate and refine the surface until it meets the desired aesthetic and functional criteria, potentially iterating between sketching, surfacing, and analysis.
3. Describe your experience with using equations and global variables to drive design changes in SolidWorks models. Can you give a practical example?
I have extensive experience using equations and global variables in SolidWorks to parametrically control designs and drive design changes. My approach involves defining key dimensions and features using global variables, which are then linked to equations. This allows for efficient modification of the model by simply changing the value of a global variable, which in turn updates all linked dimensions and features. For example, in a project involving a sheet metal enclosure, I defined global variables for overall length, width, and height (Length
, Width
, Height
). The sheet metal bend radii, flange lengths, and hole positions were then driven by equations that referenced these global variables. Changing the Length
global variable automatically updated the overall enclosure dimensions, bend locations, and hole placements, ensuring design consistency and significantly reducing rework time. This approach also facilitated design exploration by allowing me to quickly iterate through different size configurations.
4. What are the advantages and disadvantages of using configurations in SolidWorks, and how can they be effectively managed in large assemblies?
Configurations in SolidWorks offer several advantages. They allow you to create multiple variations of a part or assembly within a single file, reducing file clutter and improving organization. This simplifies design changes and allows for quick switching between different versions, like different sizes or materials. Configurations also aid in generating BOMs (Bills of Materials) for each variation and managing product families efficiently.
However, configurations also have disadvantages. Complex configurations can increase file size and rebuild times, especially in large assemblies. Managing a large number of configurations and their associated parameters can become cumbersome. To effectively manage configurations in large assemblies, best practices include: using design tables for data management, creating well-defined naming conventions for configurations, and leveraging display states to control component visibility within configurations. Employing simplified configurations or derived configurations can also reduce complexity and improve performance. Regularly reviewing and purging unused configurations is also recommended.
5. Explain the concept of design tables in SolidWorks and how they can be used to create a family of parts.
Design tables in SolidWorks are essentially Excel spreadsheets embedded within a SolidWorks part or assembly file. They allow you to control dimensions, features, and other properties of a model by defining different configurations in the table. Each row in the table represents a different configuration, and each column represents a dimension or feature parameter. By modifying the values in the table, you can quickly create a family of parts that share a common design but vary in specific dimensions or features.
To create a family of parts, you first create a base model in SolidWorks. Then, you insert a design table and specify which dimensions or features you want to control. For each configuration, you enter the desired values in the table. SolidWorks automatically generates the configurations based on the table data. This eliminates the need to manually create each part variation, saving significant time and ensuring design consistency across the family of parts.
6. How would you optimize a SolidWorks assembly for performance, considering factors such as file size, complexity, and hardware limitations?
To optimize a SolidWorks assembly for performance, consider simplifying the model by suppressing unnecessary features, using lightweight configurations, and employing display states to manage component visibility. Reduce file size by using defeatured parts where appropriate, and ensure proper use of mates to avoid over-constraining the assembly. Hardware limitations can be addressed by working with Large Assembly Mode, which optimizes graphics and memory usage, and periodically evaluating hardware upgrades for better performance. Other techniques are creating speedpaks, using level of detail, and proper configurations.
7. Describe your experience with using SolidWorks Simulation for FEA analysis. What types of studies have you performed, and what were the key findings?
I have experience using SolidWorks Simulation for Finite Element Analysis (FEA) to validate designs and predict structural behavior. I've performed various types of studies, including static stress analysis to determine stress and displacement under applied loads, frequency analysis to identify natural frequencies and mode shapes, and thermal analysis to assess temperature distribution and heat transfer. I also have some experience with buckling analysis.
Key findings often involved identifying areas of high stress concentration, predicting potential failure points, and optimizing designs to improve structural integrity and reduce weight. For example, in one project involving a cantilever beam design, static stress analysis revealed a high stress concentration at the fixed end. By implementing a fillet at that corner, the stress concentration was reduced and the factor of safety was significantly improved.
8. How would you set up a SolidWorks Simulation study to analyze the thermal stress in a component?
To analyze thermal stress in SolidWorks Simulation, first create a thermal study to determine the temperature distribution. Define the heat sources (heat generation, convection, heat flux, radiation, etc.) and boundary conditions (temperature, convection) for the component. Run the thermal study to obtain the temperature results. Next, create a static study. In the static study, under external loads, define a thermal load and import the temperature results from the thermal study previously created. Define any necessary structural restraints and loads on the component. Finally, run the static study to calculate the thermal stress based on the temperature distribution and structural boundary conditions.
9. Explain how you would use SolidWorks Flow Simulation to analyze the fluid flow around an object.
To analyze fluid flow around an object using SolidWorks Flow Simulation, I would first create or import the object's geometry into SolidWorks. Then, I'd activate the Flow Simulation add-in and create a new project. I'd define the computational domain, ensuring it's large enough to capture the flow field accurately. Next, I'd specify the fluid properties (e.g., air, water) and the boundary conditions, such as inlet velocity or pressure, outlet pressure, and wall conditions. I would mesh the domain, paying attention to refining the mesh near the object's surface where gradients are high.
After setting up the simulation, I'd run the analysis. Once completed, I'd analyze the results using various post-processing tools like cut plots, surface plots, flow trajectories, and iso-surfaces to visualize pressure, velocity, and temperature distributions. These tools help me understand the flow behavior around the object and identify areas of high drag or turbulence. Finally, I'd refine the design if necessary based on the simulation results to optimize the object's performance in the fluid environment.
10. Describe your experience with using SolidWorks PDM (Product Data Management) or other PDM systems. How does it improve collaboration and data management?
I have experience using SolidWorks PDM Professional for several projects. My primary use involved managing CAD files, engineering drawings, and related documentation. The system helped ensure everyone was working with the latest versions, preventing conflicts and rework. I routinely used features like check-in/check-out, version control, and workflow management to control the lifecycle of design data.
SolidWorks PDM significantly improved collaboration by providing a central, controlled repository for all product-related information. This eliminated the need for shared network drives and reduced the risk of using outdated or incorrect files. Features like automated workflows for approvals and notifications streamlined the design process and kept team members informed of changes. The search capabilities and metadata management also made it easier to find and reuse existing designs, saving time and effort. Overall, it boosted data integrity and team efficiency.
11. How would you manage revisions and versions of SolidWorks files using a PDM system?
Using a PDM system for SolidWorks files involves several key steps for revision and version management. First, I would configure the PDM system to automatically create new versions each time a SolidWorks file is modified and checked back into the vault. This ensures a complete history of changes. The PDM system's workflow engine can be used to manage the release process, automatically incrementing the revision number (e.g., A, B, C or 1, 2, 3) when a file transitions through approval stages like 'In Work', 'Review', and 'Released'.
Furthermore, I would leverage the PDM system's search capabilities to quickly locate specific versions or revisions of a file. Features like 'Where Used' are crucial to understand the impact of a change across assemblies and drawings. For restoring previous states, the PDM system allows easy access to historical versions, enabling a rollback if needed. Access controls within the PDM system are also essential to regulate who can modify, approve, or release files, thereby maintaining data integrity and preventing unauthorized changes.
12. Explain your understanding of Geometric Dimensioning and Tolerancing (GD&T) and how it is applied in SolidWorks drawings.
GD&T is a symbolic language used on engineering drawings to define the allowable variation in the form, size, orientation, and location of part features. It goes beyond traditional plus/minus tolerancing by controlling these variations based on functional requirements, ensuring parts fit and function as intended, improving interchangeability and reducing manufacturing costs. It focuses on how a part functions, not just how it's made.
In SolidWorks, GD&T is applied through the DimXpert tool or manually using geometric tolerance symbols found in the annotation toolbar. You select a feature (e.g., hole, surface) and then apply the appropriate GD&T symbol (e.g., flatness, position, cylindricity), along with the tolerance value and datum references. SolidWorks then visualizes these GD&T controls directly on the drawing. These GD&T callouts are linked to the model, so changes to the model may affect the GD&T scheme, which SolidWorks can help manage by flagging potentially affected GD&T features.
13. How would you create a detailed drawing in SolidWorks that accurately conveys manufacturing requirements, including GD&T?
To create a detailed SolidWorks drawing for manufacturing, start by selecting the appropriate drawing template adhering to company or industry standards (e.g., ASME Y14.5). Add all necessary views (orthographic, isometric, section) to clearly represent the part's geometry. Use the Smart Dimension tool to apply manufacturing dimensions, ensuring they are toleranced appropriately based on the part's function and manufacturing capabilities. Choose datums carefully, reflecting the functional requirements of the part.
Apply Geometric Dimensioning and Tolerancing (GD&T) symbols (e.g., flatness, cylindricity, position) to control critical features. Reference the selected datums when applying GD&T. Specify surface finish requirements using appropriate symbols and values. Add notes to clarify any ambiguous dimensions, tolerances, or manufacturing processes. Include a Bill of Materials (BOM) if the drawing represents an assembly. Finally, verify the drawing for accuracy and completeness before releasing it for manufacturing.
14. Describe your experience with creating custom features or macros in SolidWorks using SolidWorks API. What problems did you solve?
I've used the SolidWorks API with VBA and C# to create custom features and macros, primarily to automate repetitive design tasks and improve drawing generation. For example, I developed a macro to automatically generate a series of configurations for a part based on user-defined parameters like dimensions and materials. This eliminated manual data entry and reduced errors. I also created a custom feature that automatically added specific hole patterns to sheet metal parts based on predefined standards. This ensured consistency across designs and reduced design time.
One specific problem I solved involved automating the creation of detailed drawings for complex assemblies. The standard SolidWorks drawing tools were time-consuming to use for our specific assembly structure. I created a macro that iterated through the assembly, automatically generated views, added dimensions based on predefined rules, and created a bill of materials, significantly reducing the drawing creation time.
15. How would you automate a repetitive task in SolidWorks using a macro or API script?
To automate a repetitive task in SolidWorks, I'd use a macro or API script. First, I'd analyze the task to identify the repeatable steps. Then, I'd record a macro in SolidWorks while manually performing the task once. This generates a VBA script. After recording, I would edit the VBA code to make it more robust, handling potential errors and making it adaptable to different inputs or scenarios. For instance, modifying hardcoded values to accept user input, adding loops to iterate over multiple features or parts, or implementing conditional statements to handle variations.
For more complex automation, I would leverage the SolidWorks API using a programming language like VBA or C#. Key steps include:
- Referencing the SolidWorks type library in the development environment.
- Creating a SolidWorks application object:
Dim swApp As Object: Set swApp = CreateObject("SldWorks.Application")
- Accessing the active document:
Dim swModel As Object: Set swModel = swApp.ActiveDoc
- Using the API to manipulate the model, features, or properties. Error handling is crucial, using
On Error GoTo
to gracefully handle unexpected situations.
16. Explain your understanding of SolidWorks Weldments and how they are used to design welded structures.
SolidWorks Weldments provide a specialized environment within SolidWorks for designing welded structures composed of structural members and plates. Instead of modeling each individual weld, Weldments focus on defining the structural frame using predefined or custom profiles. These profiles are inserted along sketch lines and curves, creating the basic framework of the weldment. The advantage is simplified design and BOM creation, as SolidWorks automatically calculates cut lengths and generates cut lists tailored for fabrication. You can also create weld beads using weld bead feature which simplifies the representation of the weld.
Weldments also incorporate tools for adding end caps, gussets, and other supporting features commonly found in welded structures. The final output includes detailed cut lists and weld tables containing information about the materials, dimensions, and quantities needed for fabrication. You can insert these in the drawings or export them as a CSV file for manufacturing. These are easily imported by ERP systems.
17. How would you create a bill of materials (BOM) in SolidWorks and customize it to include specific information?
To create a BOM in SolidWorks, you'd typically insert a BOM table into your drawing. This can be done through the 'Insert' > 'Tables' > 'Bill of Materials' menu. After selecting the assembly drawing view, the BOM properties window appears. Here, you can choose a standard BOM template or customize it.
Customization is key to including specific information. Within the BOM properties, use the 'Columns' tab to add, remove, or reorder columns. You can link properties to custom properties defined within your parts or assembly. For example, to add a 'Material' column, you would select 'Property' under column type and then link it to the 'Material' custom property of the components. The 'Content' tab allows further customization of how the information is displayed, like formatting numbers or using conditional statements. You can also save custom BOM templates for future use, streamlining the process.
18. Describe your experience with importing and exporting files between SolidWorks and other CAD/CAM software. What challenges did you face and how did you overcome them?
I have experience importing and exporting files between SolidWorks and various CAD/CAM software packages like AutoCAD, Fusion 360, and Mastercam. I've primarily used standard formats like STEP, IGES, and STL. I've encountered challenges such as loss of feature history during translation, which required me to remodel specific features in the target software. Another challenge was dealing with surface geometry issues when converting to STL for CAM, needing to adjust tessellation settings to balance accuracy and file size. Sometimes, incompatible units would also cause scaling issues upon import, requiring careful unit conversion and verification.
To overcome these challenges, I always ensure to use the most appropriate file format for the specific software pairing and purpose. I also thoroughly inspect imported models for errors or inconsistencies, using the software's built-in tools for verification and repair. For feature loss, I attempt direct CAD-to-CAD conversions first before resorting to neutral formats. I also maintain a checklist of common issues and solutions based on previous experiences, helping me quickly troubleshoot and resolve problems during file exchange.
19. Explain how you would reverse engineer a physical part using SolidWorks, given its dimensions and material properties.
To reverse engineer a physical part using SolidWorks, I'd start by meticulously measuring all accessible dimensions of the part using tools like calipers, micrometers, and potentially a coordinate measuring machine (CMM) for complex geometries. I'd document these measurements, noting tolerances and any observed deviations from perfect geometric forms. I'd also identify the material using techniques like visual inspection (comparing to known samples), density testing, or more advanced methods such as spectroscopy if material properties are crucial.
Next, I'd create a new part file in SolidWorks and begin modeling the part based on the collected measurements. I would typically start with primary features and work my way down to secondary details. SolidWorks' sketching tools, feature modeling (extrude, revolve, sweep, loft), and surfacing capabilities would be used to replicate the part's geometry. I'd constantly compare the modeled part to the physical part and the recorded measurements, making adjustments to refine the model's accuracy. Finally, I'd verify the model's material properties in SolidWorks to match the identified material of the physical part. The reverse engineering tool in solidworks can be used for more complex shapes. After modelling, the model can be compared with scanned data of the original part to see any deviations, which can be corrected.
20. How would you use SolidWorks to design a mold for plastic injection molding?
I would start by importing the 3D model of the plastic part into SolidWorks. Then, I'd analyze the part geometry to determine the best parting line and draft angles, considering factors like undercuts and ease of ejection. Next, I'd design the mold cavity and core using SolidWorks' mold tools, including features for shrinkage compensation, runners, gates, and cooling channels. I'd also incorporate ejector pins and other necessary mold components.
Finally, I would perform mold flow analysis within SolidWorks to simulate the injection molding process, optimizing parameters like injection pressure and temperature to ensure proper filling and minimize defects. After validation, I'd create detailed 2D drawings of the mold components for manufacturing, using SolidWorks' detailing and dimensioning tools, ensuring all necessary tolerances and specifications are clearly defined.
21. Describe your experience with using SolidWorks Routing for designing piping or electrical harnesses.
I have experience using SolidWorks Routing to design both piping and electrical harnesses. My work involved creating 3D models of piping systems for fluid transfer, specifying components like pipes, elbows, and valves from the SolidWorks library or custom-designed parts. I utilized the autorouting feature to automatically generate pipe routes based on predefined rules and connection points, and then manually adjusted the routes to optimize for space constraints and manufacturing considerations.
For electrical harnesses, I've defined wire paths and selected appropriate connectors, wires, and protective coverings. I leveraged the flattening feature to create 2D harness layouts for manufacturing documentation. I have also generated bills of materials (BOMs) for both piping and electrical harness designs to ensure accurate procurement and assembly.
22. How do you handle large assembly performance issues, specifically related to graphics and rebuild times?
When addressing large assembly performance issues related to graphics and rebuild times, several strategies can be employed. For graphics performance, level of detail (LOD) techniques can be used to reduce polygon count for distant parts, along with occlusion culling to hide parts that aren't visible. Using lightweight representations (e.g., using derived parts or substituting complex features with simpler ones) can also improve performance.
For rebuild times, focus on minimizing dependencies between parts. Ensure that in-context features are used sparingly, and that features are defined as close as possible to where they are used. Consider using design tables or configurations to manage variations of parts instead of creating new parts. Evaluate the need for each feature; sometimes, a simple appearance change can eliminate the need for a complex feature. Simplifying features that are extremely complex is another area to look at.
23. What are some best practices for organizing SolidWorks files and folders to ensure efficient collaboration and data management?
Organizing SolidWorks files effectively involves establishing a clear and consistent folder structure. A common approach is to create a project-based structure, where each project has its own dedicated folder. Within each project folder, subfolders can be created for different categories of files, such as 'Parts', 'Assemblies', 'Drawings', and 'Toolbox'. Consistent naming conventions are crucial; use descriptive names that include part numbers, revisions, and descriptions. Avoid spaces in file names, using underscores instead. Utilize SolidWorks' built-in PDM (Product Data Management) tools or a dedicated PDM system to manage revisions, control access, and track changes. Regularly back up your files and adhere to a defined workflow for check-in/check-out procedures when working collaboratively. Store standard parts and templates in a shared location, ensuring everyone uses the same components and settings, and make the library read-only for general users.
Furthermore, ensure all team members understand and adhere to the defined organizational standards. Regularly audit the file structure to identify and correct any inconsistencies. Using custom properties in SolidWorks helps to embed metadata into the files which enhances searchability. Consider using configuration management tools to track changes and maintain different versions of your designs. Document your organizational standards to facilitate knowledge transfer and onboard new team members efficiently.
24. Explain the difference between a loft and a sweep feature, and provide examples of when each would be appropriate.
A loft creates a solid by transitioning between two or more profiles, blending their shapes. A sweep creates a solid by moving a profile along a path. The key difference is that a loft changes the shape of the profile along the path, whereas a sweep maintains a consistent profile shape.
Use a loft when you need to create a complex shape that morphs over its length, such as an aircraft wing or a customized bottle. Use a sweep when you need to extrude a consistent shape along a curved or straight path, such as creating a pipe, a railing, or the handle of a tool.
Expert SolidWorks interview questions
1. Describe a complex surface you've modeled in SolidWorks and the challenges you faced.
I once modeled a complex, organic-shaped motorcycle fairing in SolidWorks. The main challenge was achieving smooth, continuous surfaces while adhering to strict aerodynamic requirements. I primarily used surfacing tools like lofted surfaces, boundary surfaces, and filled surfaces, along with guide curves derived from imported styling sketches. Ensuring G2 (curvature) continuity between different surface patches was difficult, requiring careful manipulation of tangency and curvature control handles. Another significant hurdle was maintaining the desired shape while keeping the surface editable and robust; simplifying the initial sketches and using a top-down modeling approach helped.
Specifically, the area around the headlight integration was particularly tricky. I had to create several intersecting surfaces to blend the headlight housing seamlessly into the main fairing body. I used the "Knit Surface" feature extensively, but it often resulted in errors due to tiny gaps or mismatched edges. I had to repeatedly repair the model using the "Import Diagnostics" tool and manually adjust surface boundaries to achieve a watertight solid body suitable for manufacturing and CFD analysis.
2. How would you optimize a large SolidWorks assembly for performance?
Optimizing a large SolidWorks assembly involves several strategies. First, simplify components by suppressing features, using derived configurations with fewer details, or replacing complex parts with simplified envelopes or bounding boxes. Utilize lightweight graphics and large assembly mode to reduce the graphics processing load. Also, ensure proper use of mates, avoiding redundant or over-defined mates, and using patterned components instead of individual instances where appropriate.
Secondly, leverage SolidWorks' performance evaluation tools to identify bottlenecks. Evaluate mate performance and consider using speedpak configurations. For configurations, consider using display states to simplify models further. Finally, ensure appropriate hardware - a powerful CPU, dedicated graphics card, and sufficient RAM are essential for managing large assemblies effectively.
3. Explain your approach to creating parametric designs in SolidWorks.
My approach to parametric design in SolidWorks focuses on using equations, global variables, and configurations to control the model's geometry. I start by identifying key dimensions and relationships that define the design's form and function. These are then linked to global variables or equations within SolidWorks' equation manager. This allows me to easily modify these driving dimensions, and the model will automatically update, maintaining design intent. Configurations are used to define different versions or variations of the design based on these parameters.
For more complex relationships, I might use design tables to create different configurations based on an Excel spreadsheet. This is useful when dealing with a large number of variations or when the parameters are determined by external factors. Furthermore, I use relations within sketches extensively, like geometric constraints, to ensure that the intended relationships are maintained during parameter changes. This ensures robustness in the design as the model updates when the parameters are modified.
4. Discuss your experience with SolidWorks API and custom macros.
I have experience using the SolidWorks API with VBA to create custom macros for automating repetitive tasks. For example, I developed a macro that automatically generates drawings from a set of 3D models, populating title blocks and adding standard views based on predefined templates. This involved using the API to access model data, manipulate drawing views, and interact with SolidWorks' user interface.
Another project involved creating a macro to extract BOM (Bill of Materials) data from assemblies and export it to a CSV file, enabling easy integration with our ERP system. This utilized the API to traverse the assembly structure, retrieve component properties, and format the output. I'm familiar with debugging VBA code within the SolidWorks environment and have experience handling common API errors.
5. What are the advantages and disadvantages of using top-down versus bottom-up design methodologies in SolidWorks?
Top-down design in SolidWorks starts with the overall assembly layout and then defines individual parts within that context. Advantages include better control over design intent, easier management of assembly relationships, and simplified change propagation. However, it can be more complex to set up initially and requires careful planning. Bottom-up design, conversely, involves creating individual parts independently and then assembling them. This approach is simpler for basic designs, allows for part reuse, and is easier for parallel work. The disadvantages are difficulty in managing complex assembly relationships, potential for design conflicts between parts, and challenges in propagating changes across the assembly.
6. How do you handle design changes in a complex SolidWorks project?
When handling design changes in a complex SolidWorks project, I prioritize communication and documentation. First, I thoroughly analyze the change request to understand its impact on the existing design, assemblies, and drawings. This involves identifying affected components, potential interferences, and downstream effects. Then, I use SolidWorks' built-in tools like configurations, design tables, and equations to manage variations and parametric relationships efficiently. I also leverage features like FeatureManager Design Tree rollback and branch to experiment with changes without impacting the original design.
Furthermore, version control and revision management are critical. I utilize SolidWorks PDM or similar systems to track changes, manage file versions, and ensure everyone is working on the latest iteration. Before implementing any major changes, I create backups or snapshots of the project. After implementing changes, I update all relevant documentation, including drawings, BOMs, and assembly instructions. Collaboration is key, so I communicate regularly with other team members, stakeholders, and clients to keep them informed of the changes and get their feedback.
7. Describe your experience with SolidWorks Simulation and FEA analysis.
I have experience using SolidWorks Simulation for FEA analysis, primarily for static, thermal, and frequency studies. I've used it to validate designs, optimize material usage, and identify potential failure points. My workflow typically involves importing CAD models, defining material properties and boundary conditions (loads, constraints, thermal inputs), meshing the geometry, running the simulation, and then analyzing the results to generate reports and make design recommendations.
Specifically, I've worked on projects involving stress analysis of mechanical components under various loading scenarios, heat transfer analysis to optimize cooling systems, and modal analysis to determine natural frequencies and avoid resonance. I am familiar with interpreting stress contours, displacement plots, and factor of safety calculations. I've also used convergence studies to ensure the accuracy of my FEA results by refining the mesh until the solution stabilizes.
8. How would you create a sheet metal part with multiple bends and complex features in SolidWorks?
To create a sheet metal part with multiple bends and complex features in SolidWorks, I would start with a base feature, typically a sketch or a flat sheet metal part. Then, I would use the various sheet metal features like 'Base Flange/Tab', 'Edge Flange', 'Miter Flange', 'Hem', 'Sketched Bend', and 'Lofted Bend' to add bends sequentially. For complex features such as cutouts or formed shapes, I'd use the 'Cut Extrude' or 'Forming Tool' features, ensuring the features are compatible with sheet metal manufacturing practices. It's important to maintain a consistent bend radius and K-factor throughout the design for accurate flat patterns. Finally, use the "Flatten" feature to check for manufacturability and generate the flat pattern for production.
9. Explain your understanding of geometric dimensioning and tolerancing (GD&T) and how you apply it in SolidWorks.
Geometric Dimensioning and Tolerancing (GD&T) is a symbolic language used on engineering drawings and models to define allowable variation in the form, orientation, location, and runout of part features. Instead of relying solely on traditional plus/minus tolerancing, GD&T uses symbols and datums to precisely specify manufacturing requirements, ensuring parts function correctly and are interchangeable. My understanding includes concepts like datums, feature control frames, and tolerance zones, as well as the various GD&T symbols (e.g., flatness, circularity, position).
In SolidWorks, I apply GD&T using the DimXpert tool. This allows me to directly apply GD&T to the 3D model, creating feature control frames and attaching them to specific features. SolidWorks then uses this information to check for compliance with the specified tolerances. I can also generate 2D drawings with the GD&T information clearly displayed. I use datums to establish reference frames and then tolerance feature positions, orientations, forms, and profiles using the appropriate GD&T symbols and modifiers. The goal is to improve manufacturing precision, reduce scrap, and ensure functional requirements are met by defining tolerances using ASME Y14.5 standards.
10. What strategies do you use for managing configurations and design variations in SolidWorks?
In SolidWorks, I primarily use configurations to manage design variations within a single part or assembly file. This allows me to create different versions of the same design, each with potentially different dimensions, features, or materials, without creating separate files. I also leverage design tables to drive configurations based on Excel spreadsheets. This is especially useful when dealing with a large number of variations that follow a specific pattern or logic.
For more complex configurations and design variations involving different file sets or assembly structures, I utilize SolidWorks' "Configurations" or "Design Library" features. For instance, I might use "Design Library" to store pre-designed components and then drag-and-drop them into an assembly, configuring them as needed. Configurations are also useful for creating simplified versions of assemblies for FEA or visualization purposes.
11. How do you ensure data integrity and prevent errors when collaborating with multiple users on a SolidWorks project?
To ensure data integrity and prevent errors in a collaborative SolidWorks project, I'd implement a robust Product Data Management (PDM) system like SolidWorks PDM. This manages file access, version control, and workflow. Key practices include:
- Controlled Access: Define user roles and permissions to restrict who can edit specific files. Only one user should have write access at a time.
- Check-in/Check-out: Require users to check out files before editing and check them back in after making changes. This prevents concurrent modifications and potential conflicts.
- Version Control: Maintain a history of all file revisions. This allows rolling back to previous versions if errors occur. Clear commenting during check-in helps track changes.
- Defined Workflow: Establish a clear workflow process for design changes, reviews, and approvals. This ensures that all changes are properly vetted before being implemented.
- Naming Conventions: Use consistent naming conventions for files and folders to improve organization and prevent confusion.
- Communication: Encourage clear communication among team members regarding design changes and project status.
By following these practices, it reduces the risk of data corruption and promotes a smooth collaborative workflow.
12. Describe a time you had to troubleshoot a complex SolidWorks problem and how you resolved it.
In a previous role, I encountered a complex SolidWorks problem involving a large assembly that was exhibiting unexpected behavior during simulations. The assembly, a robotic arm, was failing stress tests despite seemingly adequate material properties and constraints. The initial troubleshooting steps involved checking individual component geometry for errors and verifying material assignments, but these yielded no immediate solutions.
Further investigation revealed that the issue stemmed from a combination of factors: extremely small gaps between mating surfaces in the assembly were causing solver instability, and a complex pattern of over-defined constraints. I resolved this by first using the 'Geometry Check' tool to identify and correct those tiny gaps. Next, I reviewed the assembly's feature tree and carefully adjusted constraints, replacing redundant or conflicting mates with more robust and simplified alternatives. This involved using configurations to manage the different operating states of the robot. Finally, I refined the mesh settings in the simulation, focusing on areas of high stress concentration. This combined approach stabilized the simulation and allowed us to identify and address a real weakness in the arm's design, improving its overall performance.
13. What is your experience with SolidWorks PDM or other product data management systems?
I have experience with SolidWorks PDM Professional, primarily focusing on managing CAD files, engineering drawings, and associated metadata throughout the product lifecycle. My responsibilities included creating and managing workflows for engineering change orders (ECOs), setting up user permissions and access controls, and configuring data cards to capture relevant product information. I've also worked with vault administration tasks such as backups, replication, and upgrades.
Furthermore, I have experience with Agile PLM and Windchill. This involved creating part numbers, managing BOMs, and setting up approval workflows. I've also used these systems to track revisions and document change requests.
14. How do you approach reverse engineering a physical part using SolidWorks?
Reverse engineering a physical part in SolidWorks typically involves these steps: First, accurately capture the part's geometry. This is most often done using 3D scanning techniques, like laser scanning or structured light scanning, generating a point cloud or mesh data. Import this scanned data into SolidWorks using appropriate file formats (e.g., .STL, .OBJ). Scaling, orienting, and aligning the scanned data within the SolidWorks environment is crucial for accuracy.
Then, create a solid model from the scanned data. This often requires manually creating surfaces and features that approximate the scanned geometry, using tools like Surface Fill, Lofted Surface, and Boundary Surface. Gradually build up the solid model, comparing it constantly to the scanned data to ensure accuracy. Feature recognition tools in SolidWorks can sometimes automate some of this process, especially for simple shapes. Finally, validate the model by comparing its properties (e.g., volume, mass, surface area) to the original physical part or scanned data, and refine the model as needed.
15. Explain your knowledge of different file formats supported by SolidWorks and their appropriate uses.
SolidWorks supports a variety of file formats, each suited for different purposes. Native SolidWorks formats include .SLDPRT
(part files), .SLDASM
(assembly files), and .SLDDRW
(drawing files). These formats store the complete SolidWorks feature tree and parametric data, enabling full editability within SolidWorks. Neutral formats like .STEP
and .IGES
are used for data exchange with other CAD systems, preserving the 3D geometry but not the feature history. .STEP
is generally preferred over .IGES
as it's a more modern and robust standard. Other common formats include .STL
(used for 3D printing and rapid prototyping, representing geometry as a mesh of triangles), .DXF
and .DWG
(used for 2D drawings and compatible with AutoCAD), and .PDF
(for sharing drawings and models in a portable, view-only format). .eDrawings
are also used specifically for sharing SolidWorks files in a light weight format.
The choice of file format depends on the intended use. For collaboration within SolidWorks, native formats are best. For sharing with users of other CAD systems, .STEP
or .IGES
are preferred. For 3D printing, .STL
is the standard. For sharing drawings, .PDF
or .DWG
might be suitable. The user should also consider file size, data fidelity, and the recipient's software capabilities when selecting a format. For example, a large assembly saved as .STL
will result in a very large file, whereas saving it as .STEP
and then importing it into the 3D printing slicing software can be a better option.
16. Describe your experience with creating and managing SolidWorks templates.
I have experience creating and managing SolidWorks templates for parts, assemblies, and drawings. This includes setting up standard configurations, materials, units, custom properties (for BOMs and metadata), and drawing sheet formats. I ensure the templates adhere to company standards and best practices to maintain consistency across all designs.
My process involves defining required layers, line weights, dimension styles, and annotation styles specific to the project needs. I manage these templates within a central location with version control to ensure everyone is using the most up-to-date version and track changes over time. Further, I have experience troubleshooting issues related to template corruption or inconsistencies across different user setups.
17. How would you model a part with complex draft angles and undercuts in SolidWorks?
To model a part with complex draft angles and undercuts in SolidWorks, I would primarily use a combination of surfacing and solid modeling techniques. For draft angles, I would utilize the Draft
feature, experimenting with neutral planes and parting lines to achieve the desired result. For complex geometries and undercuts, I would create surfaces using tools like Lofted Surface
, Boundary Surface
, or Swept Surface
. These surfaces can then be knitted together to form a solid body or used to cut away material from an existing solid.
Specifically for undercuts, I'd consider using a Split Line
feature combined with the draft tool or surface cut features. Sometimes, creating the undercut as a separate solid body and then using a Combine
feature with a subtract operation is effective. It's essential to analyze the part geometry and break it down into manageable features, leveraging SolidWorks' robust surfacing tools where standard solid features fall short. Feature order and careful sketching are also key for success.
18. What are your preferred methods for creating and managing library features in SolidWorks?
My preferred methods for creating and managing library features in SolidWorks involve leveraging the Design Library and configurations. To create a library feature, I typically start by designing the feature in a separate part file. I then use the 'Add to Library' command to save it to a designated folder within the Design Library. I ensure the feature is robust and easily configurable by using sketches that are fully defined and using equations or global variables to control dimensions.
To manage library features, I organize them into logical folder structures within the Design Library. I utilize configurations within the library feature part to offer variations in size, shape, or other parameters. This allows for easy selection and customization when inserting the feature into a new design. I also use the 'Feature Palette' to quickly drag and drop library features into my model. Regular maintenance, including renaming and updating descriptions, ensures the library remains well-organized and efficient to use.
19. How do you handle imported geometry from other CAD systems in SolidWorks?
When handling imported geometry in SolidWorks from other CAD systems, I typically use the Import Diagnostics tool to identify and repair any errors or gaps in the imported data. This tool helps to heal faces, knit surfaces, and close gaps to create a solid body suitable for further operations. If the geometry is complex or contains a large number of errors, I might opt to treat it as a surface body and use surface modeling tools to repair or rebuild problematic areas.
Another common approach is to use the 'FeatureWorks' add-in, which can automatically recognize features from the imported geometry. This is beneficial for editing the model parametrically, as SolidWorks can then treat the imported geometry as native features. If direct editing is needed, tools like 'Direct Editing' features can be used to modify the imported body without needing to regenerate the entire model.
20. Explain your understanding of SolidWorks equations and global variables.
SolidWorks equations and global variables are powerful tools for parametric modeling. Equations allow you to define relationships between dimensions, features, and other parameters within a part, assembly, or drawing. For example, you can set the length of a block equal to twice its width using an equation. Global variables are user-defined values that can be used in multiple equations and configurations throughout a SolidWorks model. They act as named constants. Changing a global variable automatically updates all equations that use it, ensuring design consistency and simplifying modifications.
Benefits include centralized control of key design parameters, the ability to easily explore design variations, and reduced errors during design changes. Equations can be simple formulas or complex mathematical expressions, while global variables provide a convenient way to manage frequently used values like material thickness or overall model size.
21. Describe your experience with creating photorealistic renderings in SolidWorks.
I have experience creating photorealistic renderings in SolidWorks using PhotoView 360 and SolidWorks Visualize. My workflow typically involves assigning realistic materials from the SolidWorks library or creating custom appearances, adjusting lighting (including adding HDR environments), and fine-tuning camera settings (depth of field, perspective). I also optimize models for rendering by simplifying complex features and applying appropriate surface finishes.
While using these tools, I focused on achieving realism by paying attention to details such as material properties (reflectivity, roughness), lighting effects (shadows, reflections), and post-processing techniques like adjusting brightness, contrast, and color balance within the SolidWorks rendering environment or using external image editing software.
22. How would you model a cam and follower mechanism in SolidWorks?
To model a cam and follower mechanism in SolidWorks, I would start by creating 3D models of the cam and follower as separate parts. Key considerations would be the cam profile, follower type (roller, flat-faced, etc.), and desired motion. I would then assemble these parts in SolidWorks assembly environment. A crucial step is defining appropriate mates to simulate the mechanism's motion. Specifically, I would utilize the "Cam Mate" feature, which allows you to define the relationship between the cam's curved surface and the follower. This mate constrains the follower's movement based on the cam's rotation. Finally, I would use motion analysis tools within SolidWorks to simulate the mechanism's operation, analyze its performance (e.g., follower displacement, velocity, and acceleration), and identify potential issues like interference or excessive forces. If higher fidelity or inclusion of component flex is required, a more advanced simulation like Simulia Abaqus or Ansys could be used after the initial SolidWorks model is created.
23. What are the best practices for creating and managing custom materials in SolidWorks?
Best practices for creating and managing custom materials in SolidWorks include:
- Creating a Custom Material Library: Avoid modifying the default SolidWorks material library. Create a separate, custom library (e.g.,
MyMaterials.sldmat
) to store your materials. This prevents accidental changes to the default library and simplifies sharing materials with others. You can create a new library in the SolidWorks Material dialog box by right-clicking in the material tree and selecting "New Library". - Defining Material Properties Accurately: Ensure that the material properties (density, Young's modulus, Poisson's ratio, etc.) are accurate and consistent with the intended application. Use reliable sources for material data, such as material datasheets or reputable material databases. Pay attention to units. Consider temperature dependency if relevant.
- Using Descriptive Material Names: Use clear, descriptive names for your materials that reflect their composition and grade (e.g., "Aluminum 6061-T6"). This makes it easier to identify and select the correct material for your designs.
- Specifying Appearance Properties: Define the appearance properties of your materials (color, texture, finish) to visually represent them accurately in the SolidWorks model. This improves the realism of your designs and facilitates visual communication.
- Organization: Organize your custom materials within the library using folders and subfolders based on material type, application, or other relevant criteria. A good directory structure would make them easier to search and manage.
- Backups: Regularly back up your custom material library to prevent data loss. Store the backup in a safe location, such as a network drive or cloud storage.
- Material Verification: Verify custom material properties by comparing simulation results against test data. It is important to validate material properties to ensure the reliability of simulations.
24. How do you ensure that your SolidWorks models meet specific manufacturing requirements?
To ensure SolidWorks models meet manufacturing requirements, I primarily focus on design for manufacturability (DFM) principles. This involves several key steps. First, I carefully consider manufacturing processes (machining, molding, sheet metal forming, etc.) early in the design phase and adhere to established tolerances based on those processes. I also use SolidWorks' built-in tools like interference detection, draft analysis, and feature recognition to identify potential manufacturing issues proactively. Finite element analysis (FEA) is employed to validate structural integrity and identify areas of stress concentration, ensuring the model can withstand manufacturing stresses or usage conditions.
Furthermore, I closely collaborate with manufacturing engineers and utilize their expertise to refine designs based on their feedback. This often involves design reviews where we discuss potential challenges, optimize material selection, and adjust geometry for efficient manufacturing. Finally, detailed documentation, including accurate drawings with all necessary dimensions, tolerances, and surface finish requirements, ensures clear communication with the manufacturing team.
25. Describe your experience with using SolidWorks routing for piping or electrical harnesses.
My experience with SolidWorks routing has primarily focused on piping. I've utilized it to design and model complex hydraulic systems, including specifying pipe diameters, materials (like stainless steel and PVC), and connection types such as flanges and threaded fittings. I've also worked with defining custom routing paths to avoid obstructions within the assembly and ensure proper flow characteristics. I've used the SolidWorks library to manage and insert standard piping components. I am familiar with creating custom components, like specialized manifolds or supports, and integrating them into the routing environment.
While my direct experience with electrical harnesses is limited, I understand the underlying principles of defining routing paths, assigning attributes like wire gauge and insulation type, and using connection points for components like connectors and terminals. My experience with the piping routing module has provided me a solid base to learn the harness side. I have researched SolidWorks electrical and I am confident I can use SolidWorks electrical effectively.
26. How do you approach designing parts for additive manufacturing (3D printing) in SolidWorks?
When designing parts for additive manufacturing in SolidWorks, I consider design for additive manufacturing (DFAM) principles from the outset. This includes optimizing part orientation to minimize support structures and considering build time. I analyze the part's geometry to identify potential stress concentrations and weak points, then redesign them to be more robust for the printing process. I also leverage SolidWorks' topology optimization tools to reduce material usage while maintaining structural integrity, followed by verifying the design with simulation tools. Finally, I consider tolerances and material properties to ensure the printed part meets the required specifications.
Specific considerations include: avoiding large flat areas that may warp, incorporating self-supporting angles (typically 45 degrees or greater), and designing with infill patterns in mind. Internal channels or complex geometries should be designed for easy powder removal (for powder bed fusion processes). Finally, when applicable, I design parts in an assembly to minimize the overall printing volume and reduce waste. SolidWorks has tools like the '3D Printing' tab that assist with orientation and checking minimum feature sizes.
27. What strategies do you use for creating and managing weldments in SolidWorks?
When creating weldments in SolidWorks, I prioritize a top-down design approach, starting with a 3D sketch defining the overall structure. I use the weldment feature to define structural members using standard profiles or custom profiles created in the sketch. Careful planning of sketch entities is crucial for clean corners and efficient member trimming. I use the trim/extend command extensively for corner management.
To manage weldments, I leverage weldment cut lists. I ensure correct material selection for each member to get accurate cut lengths and weights. I also focus on proper weld bead definition using weld beads feature, documenting material type, size, and length to improve manufacturing efficiency and accuracy. Final BOM includes lengths and quantities which is critical.
28. How do you handle the creation of exploded views and bills of materials in SolidWorks?
In SolidWorks, exploded views are typically created using the 'Exploded View' command within a configuration. This allows interactive positioning of components along axes or radially. Configurations can be created for each exploded state, and these can be animated. For bills of materials (BOMs), SolidWorks automatically generates them from the assembly data. I can customize the BOM by adding or removing columns, changing the quantities, and sorting the data as needed. SolidWorks also supports linking BOMs to drawings, which automatically updates the drawing BOM when the assembly is modified.
29. Explain how you would create a motion study to simulate the movement of a complex assembly.
To simulate the movement of a complex assembly using a motion study, I would typically use CAD software with motion analysis capabilities. The process involves several key steps. First, I would import the assembly model into the software and define the materials and physical properties of each component, such as mass and friction. Then, I would define the joints and constraints between the parts, specifying the types of motion allowed (e.g., revolute, prismatic, spherical). This includes setting limits on movement, like range of rotation or translation.
Next, I would apply forces, torques, or motion drivers to specific components to initiate the movement. For example, a motor providing torque to a rotating shaft. Finally, I would run the simulation, which calculates the movement of each part based on the defined physics. I would analyze the results, focusing on aspects like component collisions, stress levels, and energy consumption, and iterate on the model and simulation parameters to optimize the assembly's performance. I can often export the simulation results as a video or data file for further analysis.
30. Describe your experience with using SolidWorks Composer for creating technical documentation.
I have used SolidWorks Composer extensively to create various types of technical documentation, including user manuals, assembly instructions, and parts catalogs. My workflow typically involves importing SolidWorks CAD models into Composer, then creating high-resolution images, animations, and interactive content to clearly illustrate product features and assembly processes. I'm proficient in utilizing Composer's features such as exploded views, callouts, and bill of materials (BOM) integration to create comprehensive and easily understandable documentation.
I also have experience in customizing the output format to meet specific client requirements, including generating vector graphics for print and interactive 3D PDFs. I am familiar with updating Composer documents when design changes occur in SolidWorks, ensuring that the documentation remains accurate and up-to-date with the latest product revisions.
SolidWorks MCQ
Which sketch relation will ensure that two selected lines always remain at a constant angle to each other, even if the angle is modified?
In SolidWorks sketching, what is the primary difference between using the 'Sketch Fillet' and 'Sketch Chamfer' tools?
Options:
Which of the following is NOT a valid End Condition option when using the Extruded Boss/Base feature in SolidWorks?
Which of the following is NOT a requirement for creating a Revolved Boss/Base feature in SolidWorks?
Options:
Which Hole Wizard feature creates a hole with a countersunk shape, designed to accommodate flat-head screws?
When creating a Linear Pattern feature in SolidWorks, what does 'Direction 2' allow you to specify?
When creating a Circular Pattern in SolidWorks, which of the following parameters is NOT required to define the pattern?
When creating a Sweep feature in SolidWorks, what is the relationship requirement between the profile and the path used?
In SolidWorks, what is the primary purpose of guide curves in a Loft feature?
When creating a Shell feature in SolidWorks, which of the following parameters is NOT required?
options:
When using the Mirror feature in SolidWorks, which of the following entity types cannot be used as a mirror plane?
Which of the following is a critical requirement for creating a successful Rib feature in SolidWorks?
What is the primary function of the Draft feature in SolidWorks?
Which of the following is NOT a standard mate type in SolidWorks Assembly?
Which of the following is the MOST accurate description of how the Projected Curve feature is created in SolidWorks?
options:
When using the Fillet feature in SolidWorks, which of the following is the MOST common application for an edge fillet?
In SolidWorks assemblies, what is the primary purpose of using Interference Detection?
In a SolidWorks assembly, which of the following methods is NOT a standard way to move a component?
Which of the following end conditions for an Extruded Cut feature will cut through the entire thickness of a part, regardless of changes to the part's geometry later on?
In SolidWorks, which of the following statements best describes the functionality of the 'Offset Entities' sketch tool?
In a SolidWorks assembly, which of the following is the primary purpose of creating an exploded view?
Which of the following methods is generally used to create a curve that precisely passes through a set of predefined points in SolidWorks?
options:
Which of the following best describes the primary function of the Wrap feature in SolidWorks?
Which of the following Trim Entities options in SolidWorks allows you to trim away the sketch entity segment closest to where you click?
In SolidWorks, what is the primary function of the 'Convert Entities' sketch tool?
Which SolidWorks skills should you evaluate during the interview phase?
While a single interview can't fully reveal a candidate's abilities, focusing on key skills ensures you find a SolidWorks expert. These are the core areas to evaluate during the interview process for a SolidWorks role. By concentrating on these competencies, you'll gain valuable insights into their potential.
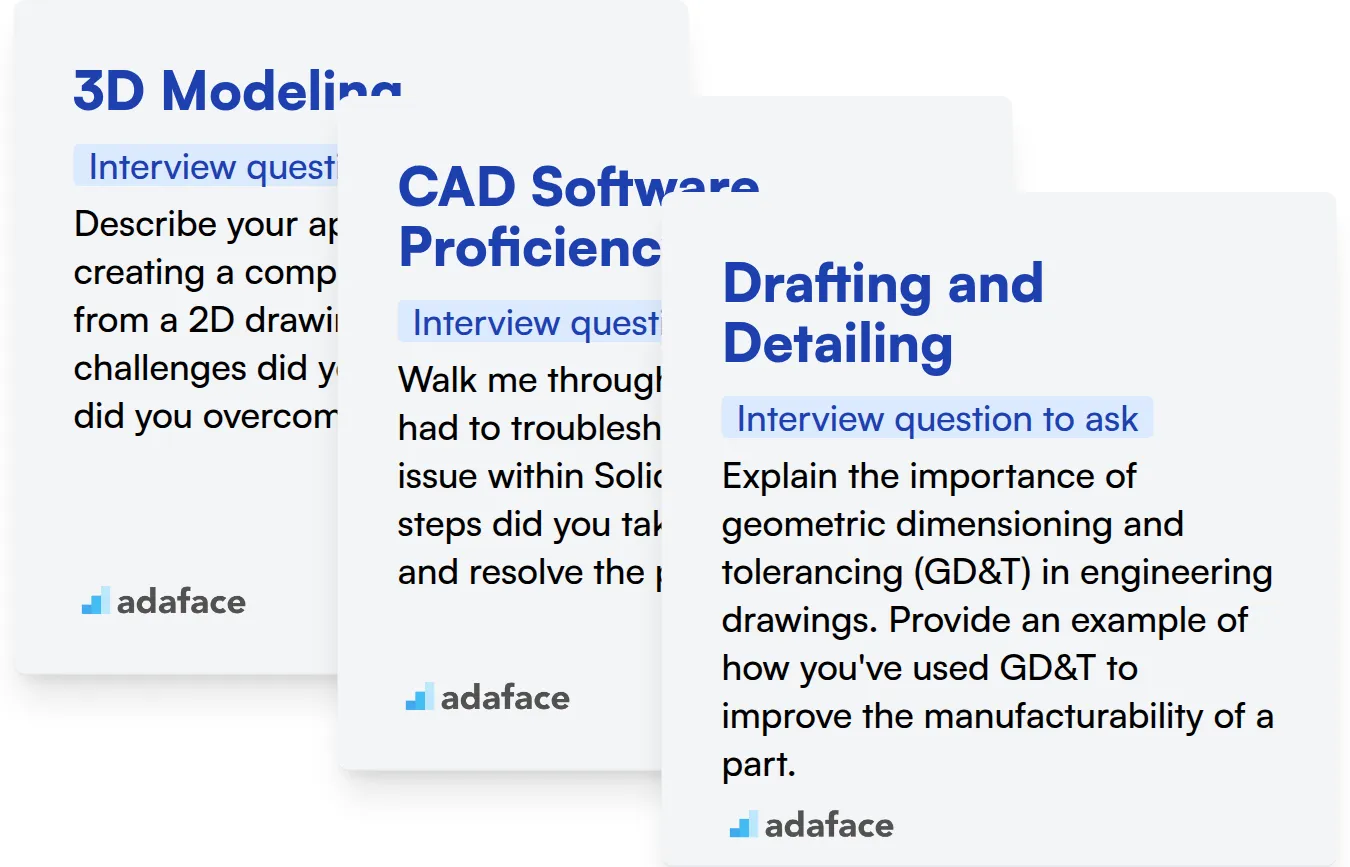
3D Modeling
An assessment test with relevant MCQs can quickly filter candidates proficient in 3D modeling. Adaface offers a Spatial Reasoning test to help you gauge a candidate's aptitude in this area.
To assess their 3D modeling skills, you can ask targeted interview questions. Let's explore a question that will help you understand the candidate's thought process.
Describe your approach to creating a complex 3D model from a 2D drawing. What challenges did you face, and how did you overcome them?
Look for a candidate who can clearly articulate their design process and problem-solving skills. They should also be able to explain the reasoning behind their design choices.
CAD Software Proficiency
You can use an assessment test with relevant questions on CAD software. Adaface offers a Technical Aptitude test which has questions on the tools and techniques.
To judge CAD software proficiency, here’s an interview question you can use. We want to learn more about their Solidworks skills.
Walk me through a time when you had to troubleshoot a complex issue within SolidWorks. What steps did you take to diagnose and resolve the problem?
The candidate should be able to describe a logical troubleshooting process, including identifying potential causes, testing solutions, and documenting their findings. Look for someone who is resourceful and persistent in their approach.
Drafting and Detailing
Here's a question to gauge their drafting and detailing expertise.
Explain the importance of geometric dimensioning and tolerancing (GD&T) in engineering drawings. Provide an example of how you've used GD&T to improve the manufacturability of a part.
Look for a candidate who understands the principles of GD&T and can apply them effectively. They should be able to explain how GD&T helps to control variation and ensure parts meet design intent. Good knowledge on this topic will also improve attention to detail.
Hire Skilled SolidWorks Professionals with Targeted Assessments
When hiring SolidWorks professionals, accurately assessing their skills is paramount. Ensure candidates possess the necessary expertise to excel in design and engineering tasks.
Skill tests offer a precise method for evaluating SolidWorks proficiency. Explore Adaface's Solid Technical Aptitude Test and Technical Aptitude Test to identify top talent.
Once you've used skills tests, you can quickly shortlist the most qualified candidates for in-depth interviews. This streamlined approach focuses your efforts on promising applicants.
Ready to elevate your SolidWorks hiring process? Visit our Online Assessment Platform or sign up to get started.
SOLID, Technical Aptitude & Coding Online Test
Download SolidWorks interview questions template in multiple formats
SolidWorks Interview Questions FAQs
Basic questions often cover interface familiarity, file management, sketching, and basic feature creation like extrudes and revolves.
Intermediate questions typically involve assembly constraints, part configurations, sheet metal design, and working with equations.
Advanced questions might explore surfacing techniques, weldments, mold design, API usage, and simulation/analysis capabilities.
Expert questions could cover complex assembly management, advanced simulation scenarios, custom feature development, large dataset handling, and performance optimization.
They help assess a candidate's practical SolidWorks skills, problem-solving abilities, and overall understanding of CAD principles.
Look for a combination of technical proficiency, problem-solving skills, attention to detail, and the ability to work collaboratively within a team.
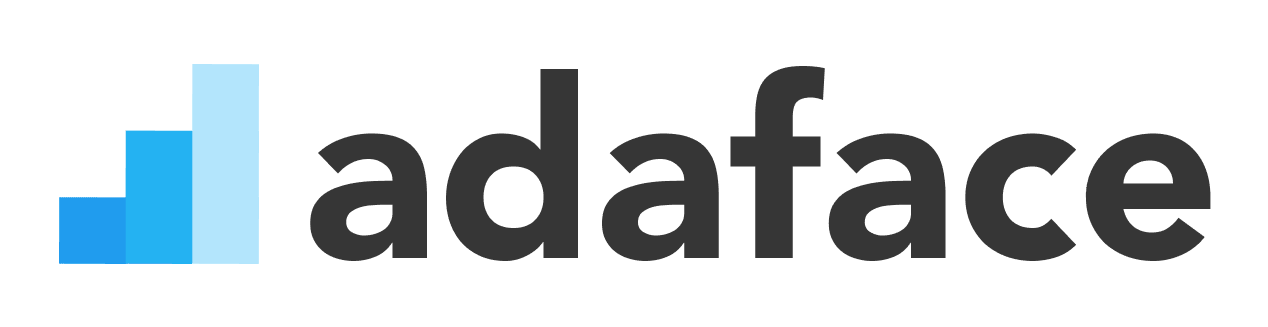
40 min skill tests.
No trick questions.
Accurate shortlisting.
We make it easy for you to find the best candidates in your pipeline with a 40 min skills test.
Try for freeRelated posts
Free resources
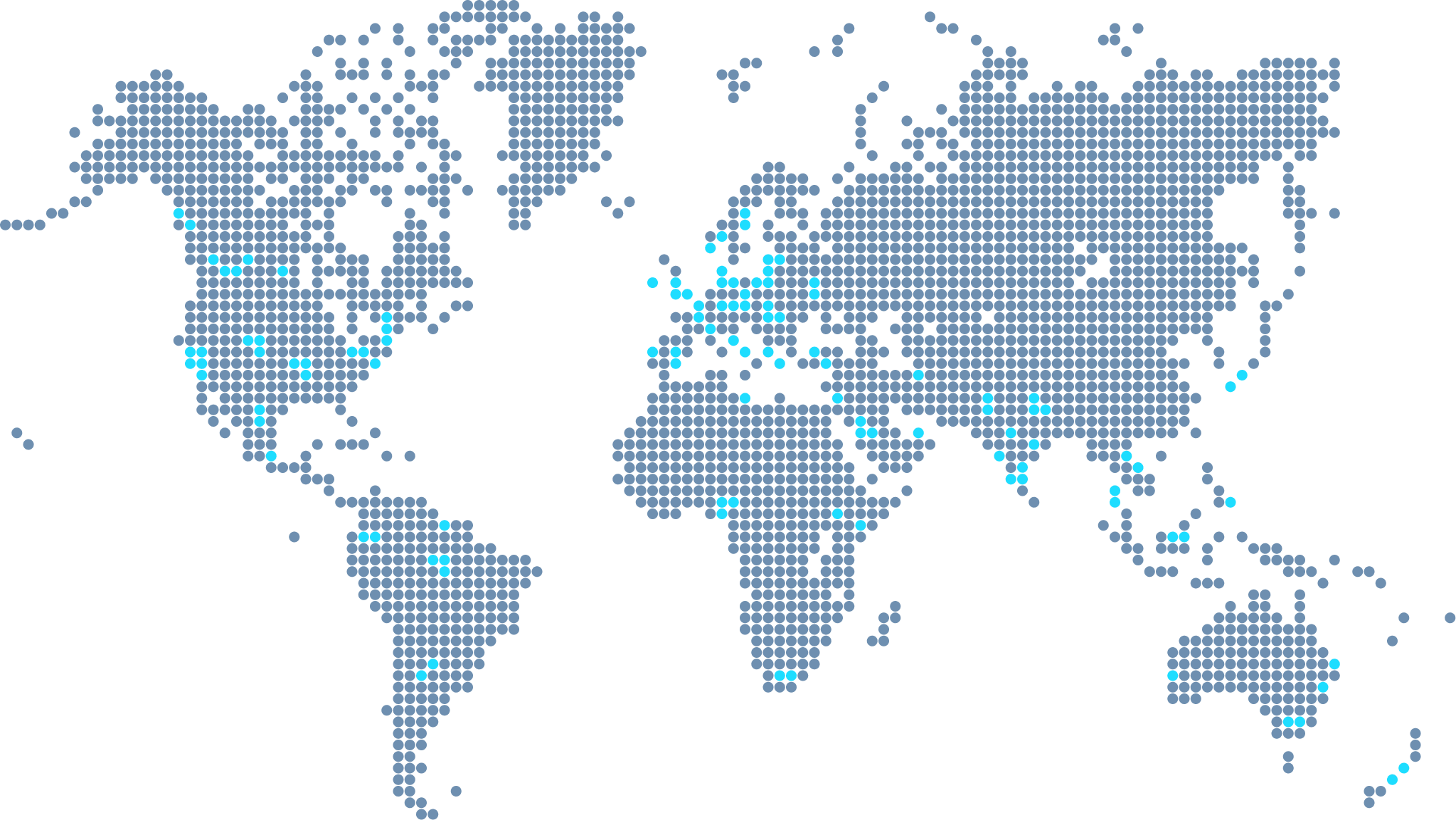
